El moldeo por inyección de piezas de automoción es el proceso de inyectar material fundido en un molde para crear piezas complejas, principalmente de plástico. Esta técnica es ampliamente aceptada en la fabricación de automóviles, ya que crea un gran volumen de piezas con una precisión superior. La función del moldeo por inyección para aplicaciones de automoción se caracteriza por su eficacia y versatilidad.
Permite a los fabricantes producir numerosas piezas de automóvil, externas e internas, como parachoques y paneles, e internas y complejas, como el salpicadero y los embellecedores. Además, define un proceso que ha reducido el tiempo y el coste de producción.
El moldeo por inyección ha abierto el uso de diferentes materiales, como los plásticos ligeros, que contribuyen al consumo de combustible y reducen el peso total del vehículo. A medida que avanza el sistema de producción de automóviles, el moldeo por inyección sigue siendo una parte esencial del proceso de crecimiento.
La fabricación justo a tiempo consiste en producir piezas a tiempo y a bajo coste. Es crucial para hacer frente a la rápida evolución de las especificaciones de los vehículos modernos gracias a inventos como los coches eléctricos y los dispositivos de seguridad avanzados.
El moldeo por inyección es vital para mejorar las prestaciones, el aspecto y el impacto medioambiental de los vehículos de la industria automovilística.
Visión general del proceso de moldeo por inyección en piezas de automoción
El moldeo por inyección de piezas de automóvil comienza con la preparación del material, incluidos los gránulos o pellets de plástico. Mientras preparan estos materiales, los técnicos los secan para eliminar la humedad del agua. A continuación, mezclan en los gránulos secos el colorante y otros componentes vitales que necesitan los clientes.
Tras la preparación, los técnicos colocan la materia prima en una máquina de moldeo por inyección. El molde calienta el material para que se funda. A continuación, dirigen las gotitas de plástico a un molde cerrado aplicando una presión considerable para cubrir todas las hendiduras de la cavidad o forma del molde.
Tras la inyección de la masa fundida, se inicia una fase de enfriamiento. El enfriamiento se produce en los canales de refrigeración del molde por los que circula refrigerante para congelar el plástico. Una vez enfriado, el material adopta la forma del molde.
En esta fase, los técnicos utilizan las clavijas o placas eyectoras para expulsar la pieza final. El producto pasa a la inspección de calidad para ver si hay algún fallo y asegurarse de que la pieza es de la calidad adecuada.
En la industria del automóvil, el moldeo por inyección es vital para crear componentes robustos, precisos y de alto rendimiento. El sector cuenta con formas y geometrías sofisticadas para las distintas piezas de los automóviles. El moldeo por inyección ayuda a lograr la repetibilidad en la producción.
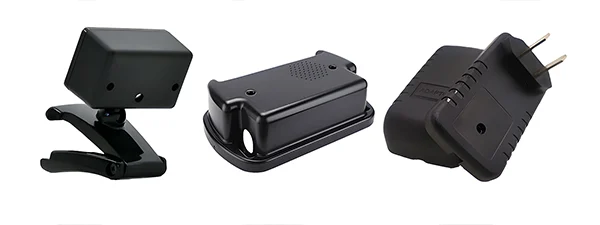
Ventajas críticas del moldeo por inyección para piezas de automoción
El moldeo por inyección desempeña un papel crucial en la fabricación de las piezas motrices. Este método tiene varias ventajas sobre los procesos de fabricación convencionales, como la eficiencia.
Alta eficiencia productiva
Una de las principales ventajas del proceso de moldeo por inyección es su alta eficiencia productiva. Permite producir un gran número de piezas por vez. Esta alta eficiencia productiva depende de la rapidez de los tiempos de ciclo y de la automatización.
Tras fabricar los moldes, el moldeo por inyección puede fabricar las piezas repetidamente y con rapidez. La duración de la producción es baja, de unos segundos a unos minutos por inyección, según el tipo de pieza y el material plástico.
El proceso requiere un trabajo manual mínimo, lo que reduce al mínimo los posibles errores humanos. Además de beneficiarse de una gran precisión, la automatización de los sistemas permite gestionar la alimentación, inyección, refrigeración y expulsión de los materiales. Este enfoque, a su vez, mejora la producción.
Flexibilidad de diseño
Este proceso de fabricación ofrece una libertad de diseño casi ilimitada en comparación con otros procesos de fabricación. La flexibilidad de este proceso de fabricación tiene que ver con la densidad geométrica, la densidad del material y el grado de personalización. Técnicas como el moldeo multimaterial o por coinyección permiten a los fabricantes utilizar distintos materiales y producir piezas con características y propiedades disímiles.
Por ejemplo, la integración de termoplásticos rígidos con otros materiales más blandos al tacto puede mejorar la utilidad. El proceso posibilita la personalización, lo que permite a los fabricantes crear una pieza distinta ideal para un modelo concreto de coche o cliente.
Relación coste-eficacia
El coste de adquisición inicial del equipo de moldeo por inyección y la creación de moldes puede ser costoso. Sin embargo, el proceso reporta más beneficios. Debido a los elevados gastos iniciales, el moldeo por inyección se ha vuelto económico para las producciones a gran escala. En este proceso de fabricación, el coste por unidad disminuye a medida que aumenta el número de unidades fabricadas. Esto supone una ventaja para la fabricación de piezas de automoción.
Una cosa que merece la pena destacar es la exhaustividad del moldeo por inyección, ya que sólo utiliza unos pocos materiales. Los fabricantes pueden reciclar los restos del proceso, ahorrando en el coste de las materias primas.
La automatización del proceso puede reducir significativamente los costes de mano de obra al disminuir el número de empleados que manejan el equipo.
Calidad constante
El uso del moldeo por inyección en piezas de automoción genera productos de alta calidad y aumenta la uniformidad en las siguientes series de producción. Todas las piezas se fabrican en circunstancias similares, incluidas sus dimensiones y partes. Esta fiabilidad es fundamental en la industria emotiva, donde las medidas de seguridad y el alto rendimiento son esenciales.
Piezas comunes de automoción producidas mediante moldeo por inyección
El proceso de moldeo por inyección permite la formación de formas complejas y confiere precisión y capacidad para hacer frente a una mayor producción. Es apropiado para distintos elementos de un automóvil. A continuación encontrará una lista de piezas de automoción comunes fabricadas mediante moldeo por inyección:
Luces del coche (faros delanteros y traseros)
Las lentes de plástico transparente de los faros delanteros y traseros de los coches son producto del moldeo por inyección. La fabricación de estos componentes requiere un alto grado de precisión y claridad debido a la importancia de la transmisión de la luz y la seguridad. Estas luces deben ser capaces de sostener y soportar impactos y condiciones meteorológicas extremas. Tales condiciones incluyen heladas, nieve, precipitaciones y luz solar abrasadora. Los requisitos de fabricabilidad del moldeo por inyección permiten diseñar libremente el grosor de las piezas en amplitud y frecuencia, ajustándose a dichas densidades.
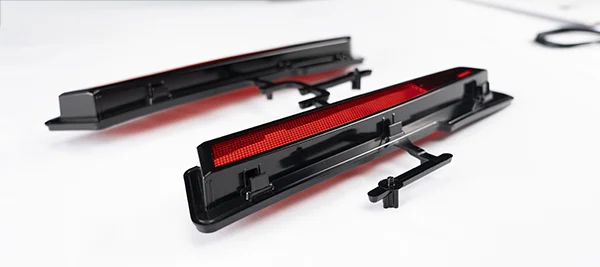
Tiradores de puerta
La mayoría de las manillas de las puertas son productos moldeados por inyección, ya sean interiores o exteriores. Este proceso permite dar una forma refinada a la pieza e integrar un diseño ergonómico. Las manillas de las puertas deben ser robustas y elegantes, ya que se utilizan en aplicaciones que requieren muchos ciclos. El moldeo por inyección permite combinar materiales. Los fabricantes pueden utilizar una base de plástico rígido para el contenedor y un material más blando para fabricar la manilla.
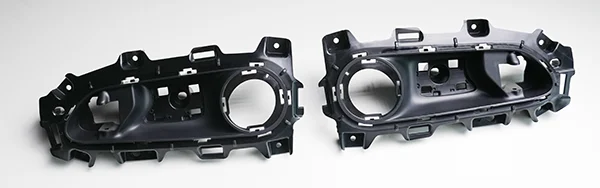
Parachoques
Los parachoques de los automóviles son grandes elementos estructurales que protegen a los vehículos de los impactos y son producto del moldeo por inyección. El proceso es ideal para fabricar piezas de refuerzo críticas para cualquier ensamblaje de automóviles. Los parachoques de los coches deben ser resistentes para proteger el vehículo en caso de accidente. La selección adecuada de materiales para el parachoques es esencial, ya que contribuye a los precios del vehículo. El moldeo por inyección ayuda a producir parachoques con la resistencia correcta y con un alto nivel de precisión.
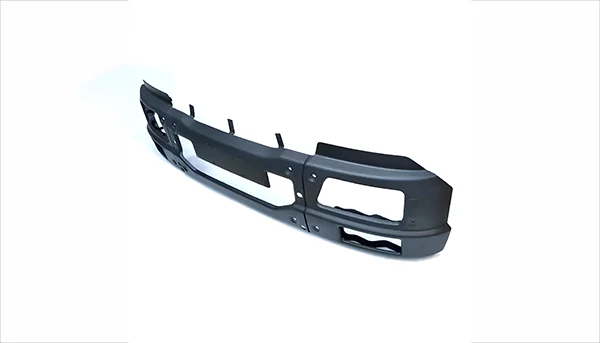
Cuadros de mando
Los salpicaderos son productos grandes y polifacéticos del moldeo por inyección. Contienen biseles, botones, interruptores, diales, otros indicadores y otros componentes de seguridad como los airbags. Según el tipo de coche, el salpicadero debe tener un acabado agradable y ser lo bastante resistente para soportar el uso diario. Como su nombre indica, el moldeo por inyección es un proceso que consiste en inyectar material en un molde.
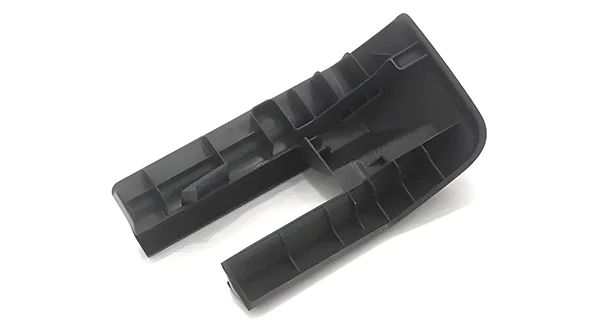
Piezas interiores
El moldeo por inyección forma las piezas de revestimiento interior, incluidos los paneles de las puertas, la consola central y los asimiladores del salpicadero. Estos componentes hacen atractivo el interior del vehículo y tienen otros usos. Las piezas de guarnecido deben ser ligeras a la vez que duraderas y capaces de adaptar elementos de textura, color y acabado coordinados y contrastados. El moldeo por inyección también ofrece la integridad, la estética y la ergonomía necesarias para este estilo.
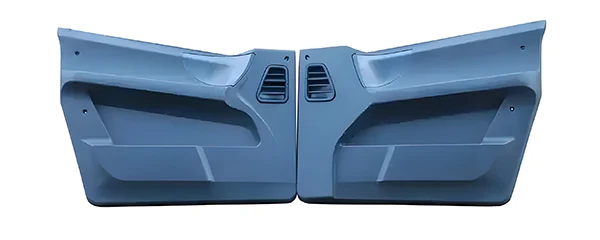
Rejillas
Las rejillas tienen aplicaciones prácticas como dispositivos de refrigeración del motor y forman parte del diseño de la fachada del automóvil. El moldeo por inyección garantiza que estas piezas sean duraderas y estéticamente atractivas.
Rejillas de ventilación y componentes HVAC
Las rejillas de ventilación del interior del automóvil y otras piezas del sistema de climatización de un coche son productos habituales del moldeo por inyección. Requieren especificaciones más finas para permitir la cantidad óptima de flujo de aire y regular la temperatura. El moldeo por inyección permite crear componentes de climatización.
Tapas de motor
Las cubiertas del motor se moldean por inyección para proteger las piezas esenciales del motor de la suciedad y el calor. Estas cubiertas requieren una selección adecuada del material de sellado. Deben ser ligeras, resistentes al calor y duraderas. El moldeo por inyección garantiza que posean estos requisitos funcionales al tiempo que absuelve la apariencia de elegancia.
Cajas de fusibles y carcasas eléctricas
Las cajas y armarios protegen las delicadas piezas eléctricas del colapso físico, la humedad y los residuos. Todas estas piezas requieren una gran precisión y capacidad. Por ello, el moldeo por inyección es el proceso de fabricación preferido para estos componentes. Además, permite utilizar diseños ap-fit para construir el modelo y facilitar la interconexión.
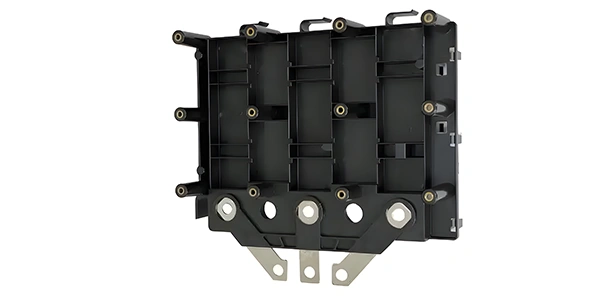
Revestimientos de pasos de rueda
El moldeo por inyección produce revestimientos de pasos de rueda. Estos revestimientos cubren los pasos de rueda del vehículo y evitan que entren en contacto con el barro, la suciedad o los residuos. Estas piezas deben ser lo suficientemente rígidas y dúctiles como para soportar la exposición diaria a las condiciones más duras de la carretera. A la inversa, deben ser capaces de soportar la sobrecarga del vehículo.
Guarniciones para pilares
El moldeo por inyección produce los pilares estructurales del interior de un vehículo guarnecido con guarniciones de pilares. Este proceso permite un ajuste y una apariencia adecuados. Estos subconjuntos desempeñan un papel importante en el aspecto del interior del vehículo y enmascaran componentes de seguridad como los airbags.
Tipos de material utilizados en el moldeo por inyección para automóviles
El moldeo por inyección para automóviles puede adaptarse a una gran variedad de materiales para producir una pieza que tenga las características deseables de resistencia y resistencia al calor. Algunos ejemplos son diversos tipos de plásticos y compuestos que proporcionan características distintivas para satisfacer un requisito específico de los automóviles. A continuación se ofrece una visión general de los materiales más comunes y su relevancia para la industria del automóvil:
Polipropileno (PP)
El PP es un tipo de termoplástico con una estabilidad química extrema, un peso relativamente bajo y una elasticidad notable. Es habitual en revestimientos interiores y exteriores de automóviles, como parachoques, salpicaderos y paneles de puertas. Tiene una baja densidad y una alta resistencia al impacto, lo que no garantiza que el material se agriete con facilidad. El PP es más rentable y mecánicamente superior a otros polímeros por su flexibilidad y durabilidad, por lo que es adecuado en aplicaciones en las que las piezas sujetas experimentan un uso intensivo.
Acrilonitrilo butadieno estireno (ABS)
El ABS es un termoplástico de alta resistencia y gran durabilidad, con gran tenacidad, resistencia al impacto y excelente rigidez. Una aplicación popular del ABS en automoción son las piezas de revestimiento interior, las intervenciones en salpicaderos y las consolas. Su superficie brillante lo hace adecuado para el aspecto de piezas de automóviles y otros vehículos que requieren piezas pulidas. El ABS también es habitual en aplicaciones de interior de automóviles por su fino aspecto y su gran resistencia al impacto.
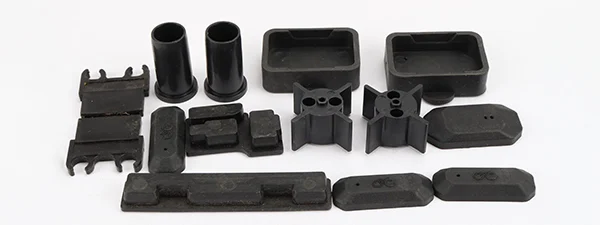
Poliamida (nailon)
El nailon tiene buenas propiedades mecánicas, como resistencia al desgaste y a altas temperaturas. También tiene una buena resistencia química a diferentes fluidos de automoción, como el aceite y el combustible. El nailon es habitual en muchas piezas bajo el capó, como los capós del motor, las tomas de aire y los embellecedores del sistema de combustible. Sus elevadas características térmicas y mecánicas justifican su aplicación en piezas con altas temperaturas y cargas mecánicas.
Policarbonato (PC):
El policarbonato es conocido por su gran resistencia a los impactos y su claridad; se utiliza a menudo cuando la aplicación requiere seguridad y claridad. Es ligero pero muy robusto, lo que le confiere un gran valor en cuestiones de seguridad. Otras aplicaciones típicas del PC son las molduras interiores y exteriores de automóviles, como las lentes de faros delanteros y traseros, techos solares y techos panorámicos. El policarbonato es, por tanto, adecuado para fabricar piezas que deben ser transparentes y robustas, como las luminarias de los automóviles.
Elastómeros termoplásticos (TPE):
Los TPE incorporan los atributos de los plásticos en su procesamiento, al tiempo que portan la flexibilidad y elasticidad del caucho. Soportan bien la resistencia, la rotura y las temperaturas fluctuantes. Los TPE se aplican a sellos, juntas y componentes aislantes de vibraciones. Son útiles en piezas en las que se desea flexibilidad y alto rendimiento. Los materiales TPE son necesarios cuando el componente debe tener una flexibilidad constante y una estabilidad dimensional en relación con la temperatura. Entre las posibles áreas de aplicación se incluyen los umbrales de puertas y los canales de ventanas.
Conclusión
El moldeo por inyección es una tecnología esencial para la producción de piezas de automoción. Crea piezas complicadas de alta calidad con precisión y rapidez. Gracias a su flexibilidad, es barato y produce casi cualquier pieza del automóvil.
El proceso abastece al creciente mercado de materiales de resistencia ligera que pueden mejorar la dinámica del vehículo y un mayor ahorro de combustible.
Los avances tecnológicos como la Industria 4.0, la automatización y la fabricación aditiva son esenciales en el moldeo por inyección de automóviles. Mejoran la eficiencia y reducen los costes, los plazos de entrega y aumentan la calidad.
El futuro busca lanzar al mercado compuestos avanzados y plásticos de base biológica que permitan desarrollar nuevas estructuras de automoción ligeras y sostenibles. Además, la aplicación de tecnologías inteligentes e impresión 3D al moldeo por inyección convencional creará nuevas oportunidades y variabilidad adicional.
Recomendación
Para conocer mejor algunos de los retos y puntos críticos de la producción de piezas de automoción, visite nuestro "sección de fabricación de piezas de automóvil". Esta página ofrece una visión general de muchos componentes para automóviles fabricados mediante servicios de moldeo por inyección, como lentes, tiradores de puertas y embellecedores interiores, etc.