PBT (Polybutylene Terephthalate) Injection Molding
High strength and stiffness PBT plastic solution
- Excellent electrical insulation for electrical and electronic components
- Glossy appearance for visible parts
- Rapid and precision injection molding cycles
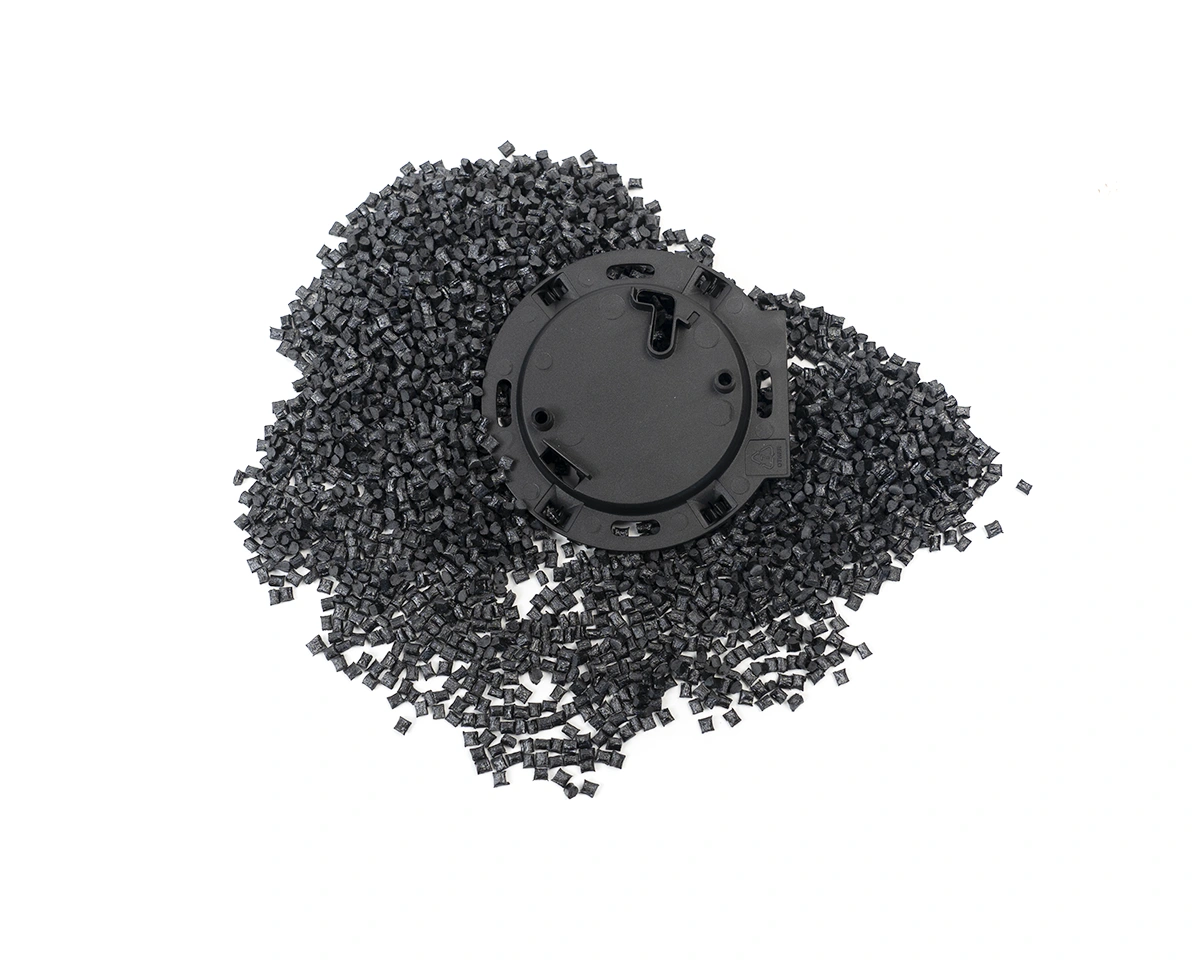
FirstMold's PBT Injection Molding Capabilities
FirstMold possesses comprehensive knowledge and experience in PBT injection molding, including various modified PBT materials. Our mold designers have extensive capabilities in product analysis and understanding user requirements, combined with precise mold CNC machining and on-site production management skills, enabling us to create products that exceed your expectations in PBT injection molding.
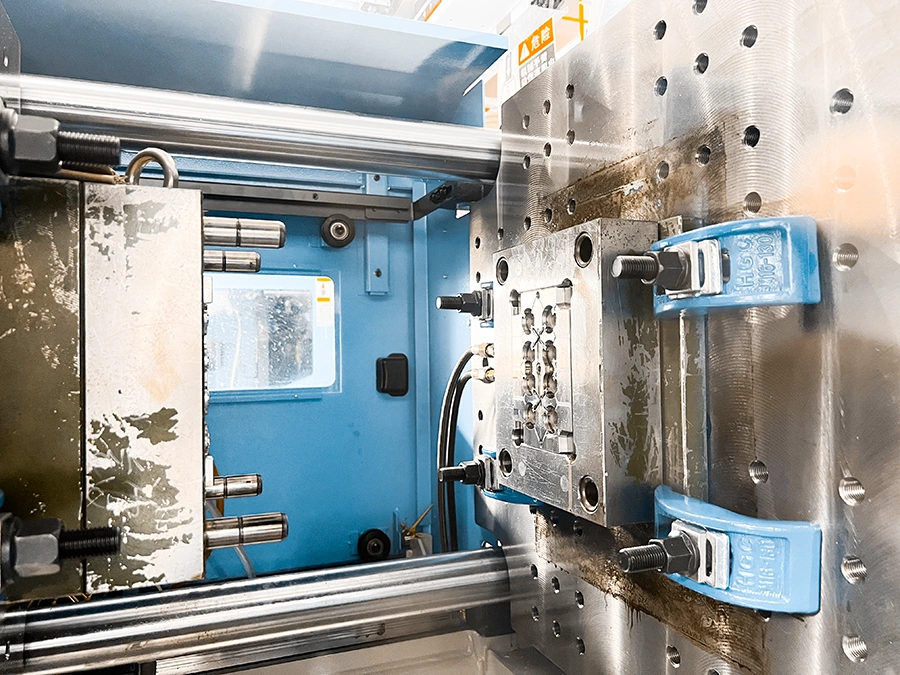
Applications of PBT Injection Molding
Although PBT does not feel as smooth as ABS and has poorer light transmission compared to ABS, PBT has carved out a niche in the keycap market against ABS keycaps thanks to its superior durability and oil resistance.
Automotive & EV
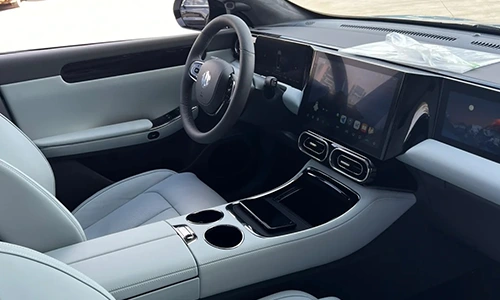
- Connector systems
- Sensor housings
- Junction blocks
- Headlamp bezels
- Door handle mechanisms
- Electrical mirror adjusters
- Thermostat housings
Electrical
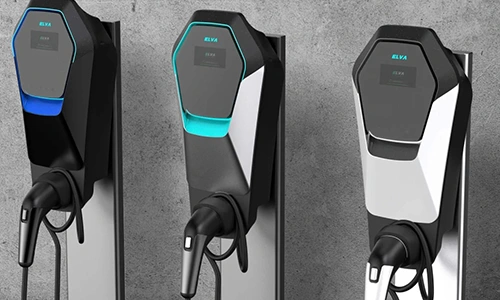
- Circuit breaker components
- Switchgear parts
- Relay casings
- Plugs and sockets
- Light switch components
- Mounting bases
- Housings for electrical meters
Electronic
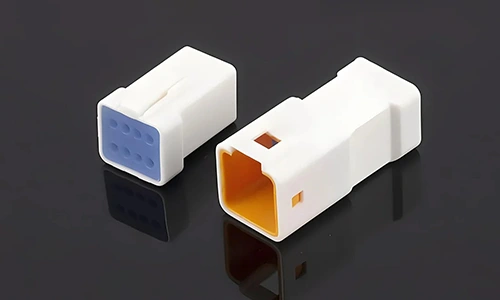
- PCB mounts
- Bobbin and coil formers
- Electronic housings requiring EMI/RFI shielding
- Keyboard keycaps
- Electronic gears and cams
- USB connectors
- Control knobs
Home Appliances
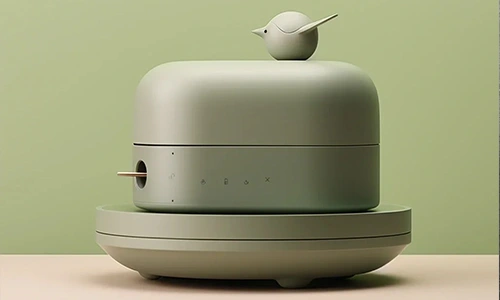
- Control panels and buttons
- Coffee machine components
- Blender bases and gears
- Air conditioner control housings
- Range hood filters and frames
- Humidifier tanks and caps
- Fan blades and housings
The modifications of PBT mainly include flame-retardant PBT, glass fiber-reinforced flame-retardant PBT, and glass fiber-reinforced PBT. PBT is commonly blended with PC to form alloys used in automotive parts, with PC/PBT often utilized for car bumpers. Additionally, modified PBT can be used for car window motor housings, motorcycle motor parts, and automotive transmission gearboxes.
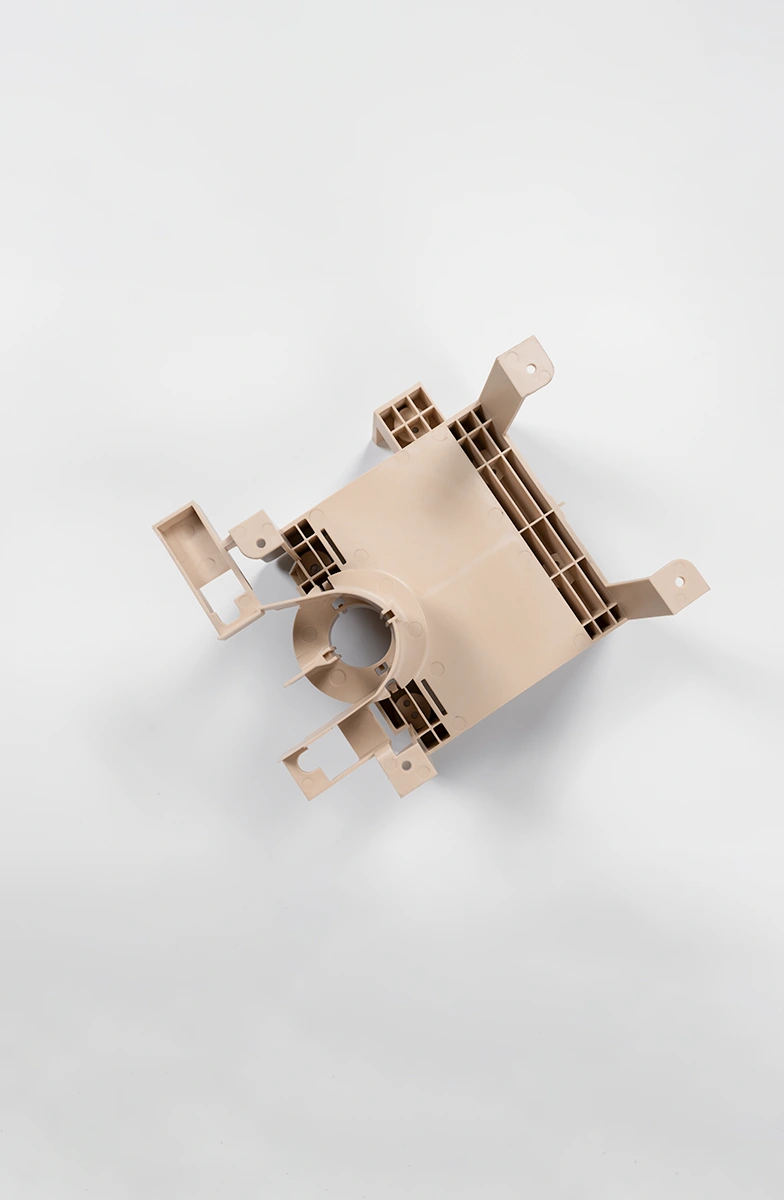
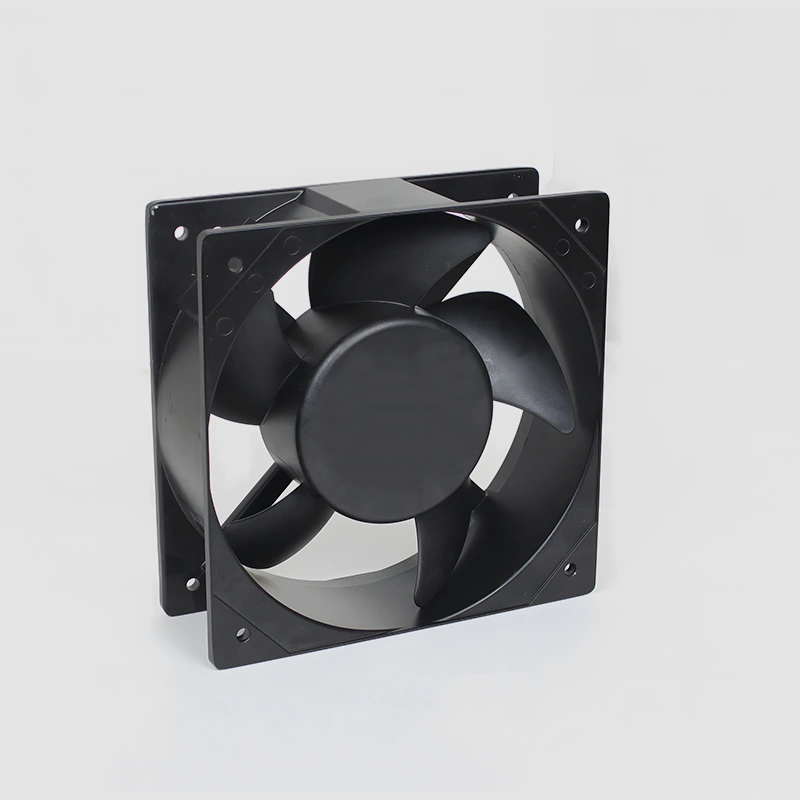
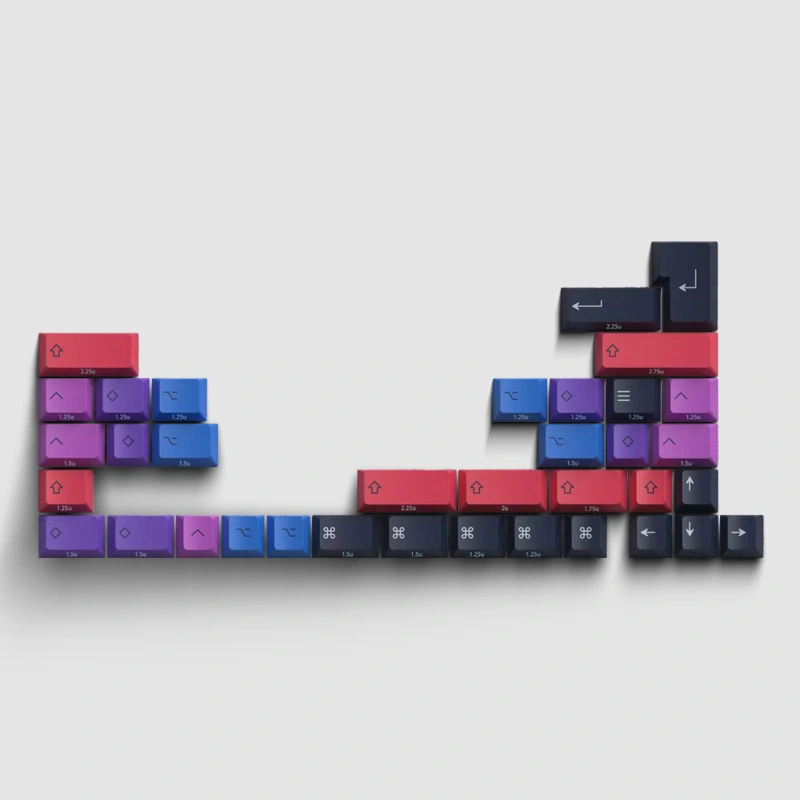
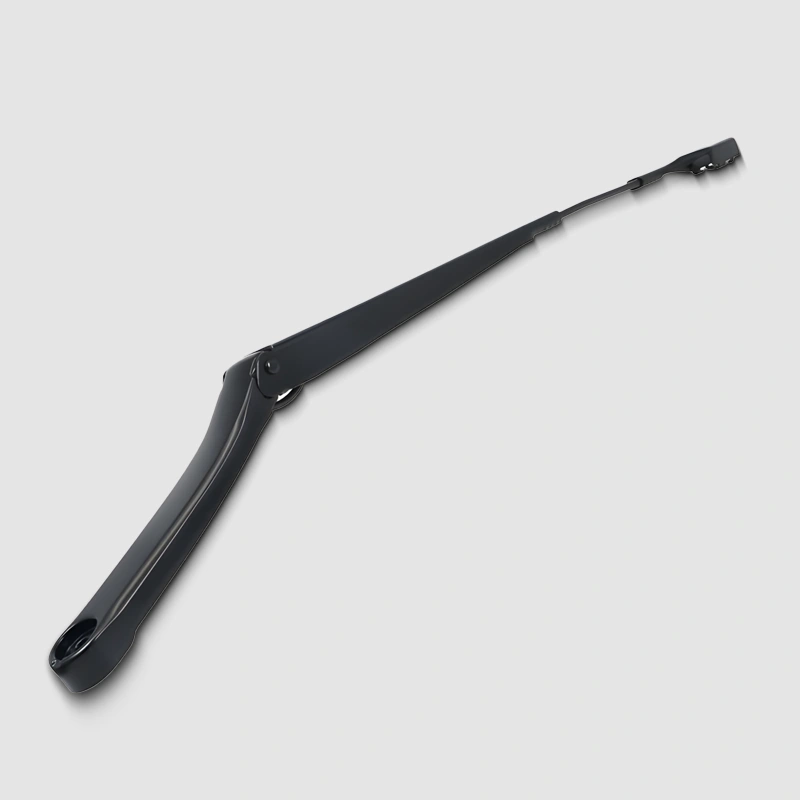
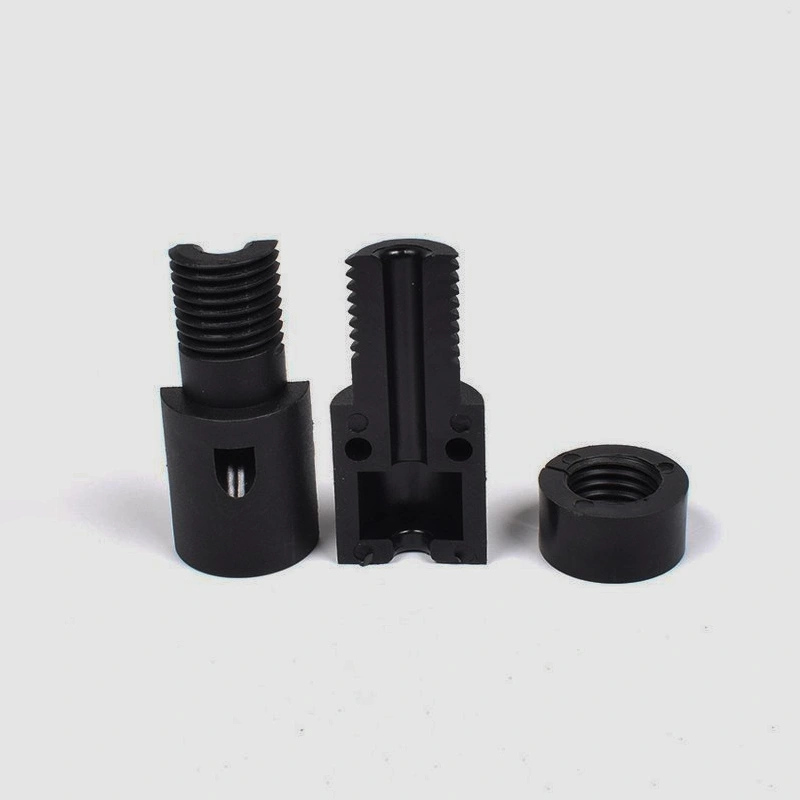
聚丙烯
PE
个人电脑
聚氯乙烯
ABS
PA
POM
PBT
PMMA
PEEK
PBT Products Quality Assurance
The quality of PBT plastic fabricated products is inseparably linked to the quality of the raw materials used. We have stable suppliers with whom we’ve cooperated for over a decade, and we can provide quality inspection reports for any raw materials. We can also purchase from suppliers you specify and provide proof of purchase.
Advanced Mold Testing
FirstMold conducts mold fitting and mold polishing for every set of molds and performs mold testing using precision CNC machines, precision injection molding machines, and mold fitting machines.
In-Process Quality Checks
FirstMold implements 6S management on-site, promptly addressing any issues that arise at each stage. Injection molding production also includes timely spot checks, along with immediate preventive measures and quality control adjustments.
Final Inspection and Testing
Comprehensive final quality inspections are conducted using professional testing equipment, including coordinate measuring machines (CMM), height gauges, moisture analyzers, pressure gauges, and color controllers, to ensure the utmost quality.
Advantages of ABS injection molding
Through the various features of ABS injection molded parts, we can easily understand the multiple advantages of ABS injection molding.
- Durability and Precision: ABS injection molded parts provide the necessary impact resistance, dimensional stability, and precision required for components like dashboards and bumpers, durable casings and intricate components.
- Aesthetic Versatility: These parts can be finished to a high-quality appearance, suitable for toys and appliances that require an attractive look, as well as healthcare devices where functionality combines with user-friendly design.
- Cost-Efficient Production for High-Volume Industries: The ease of processing and recyclability of ABS make it ideal for industries like construction and packaging, where cost efficiency and the ability to produce large quantities of durable, precise parts are critical.
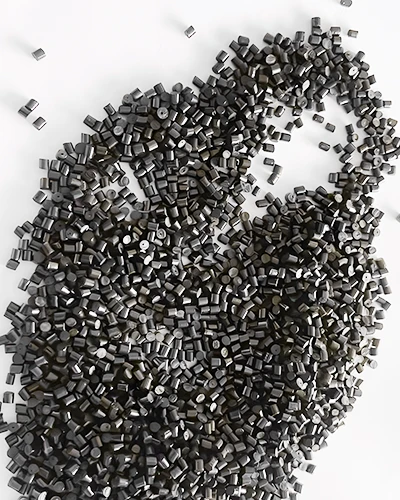
According to statistics, ABS material has the highest usage rate in all injection molding projects at FirstMold.
PBT Injection Molding Cases
This case shows the insert molding process to produce drone remote control housing from a Chinese plastic component manufacturing factory
This study shows the molding manufacturer's capabilities to manufacture perfect fuse holder base parts with precision injection molding.
FAQs For PBT Plastic Fabrication
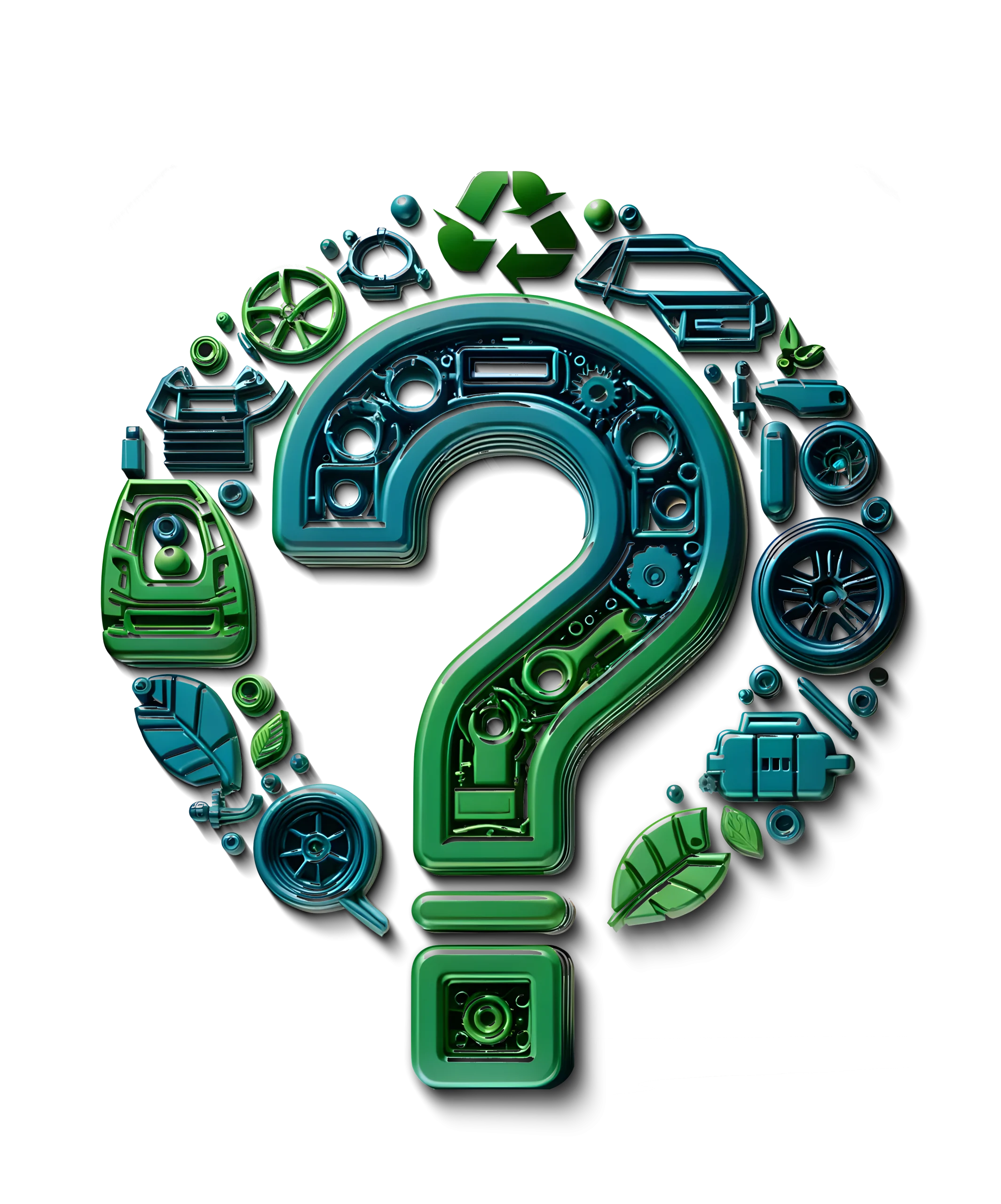
What is PBT injection molding?
PBT injection molding is a plastic processing method that involves feeding plastic raw materials into an injection molding machine, where the plastic is melted under high temperature and pressure, and then molded into the desired shape through a mold.
Polybutylene Terephthalate injection molding has higher production efficiency, excellent mechanical properties, and high-temperature resistance compared to other plastic molding methods. The difference from other plastic molding methods is that PBT injection molding requires higher injection pressure and mold precision to obtain high-quality plastic parts.
Additionally, PBT injection molding requires the plastic raw materials to have good fluidity and thermal stability to ensure a smooth processing procedure.
To find out how it works, about its benefits, and on its applications of it in detail, we invite you to find out our well explained guide. This link will direct you to further information on injection molding: WHAT IS INJECTION MOLDING?
How long do PBT injection molding projects typically take at FirstMold?
The duration of PBT plastic fabrication projects at FirstMold varies with the complexity of the project. For simpler projects, the entire production cycle may be relatively short, usually ranging from a few weeks to a few months.
For more complex projects, more time may be required to design and manufacture the molds, as well as to carry out production and testing. Generally, projects with higher complexity may require more time to meet design and performance requirements.
What typically includes in the pricing structure for PBT injection molding services?
Factors that affect the cost of the project include the complexity of the project, the production cycle, quality requirements, and the market price of raw materials.
The higher the complexity of the project, the more design and development time may be needed, and the pricing will correspondingly increase.
The longer the production cycle, the more equipment and labor costs will be consumed, and the pricing will also increase accordingly.
Additionally, higher quality requirements might necessitate more quality control and testing steps in the production process, which will also affect pricing.
Furthermore, changes in the market price of raw materials will directly impact the cost of the project, thereby affecting the pricing.
What are the design guidelines for PBT injection molding?
The design guidelines for PBT injection molding include performance requirements such as the strength, stiffness, heat resistance, and chemical corrosion resistance of the product, as well as factors such as the structure, size, material, and cooling system of the mold.
In terms of wall thickness design, it should be as uniform as possible to ensure uniform molding and stability of the plastic parts.
For draft angles, it is usually necessary to consider the properties of the plastic and the structure of the mold to ensure the longevity and stability of the mold. The design of the gate location should be based on the structure and process requirements of the plastic parts to achieve the best filling and cooling effects.
Additionally, the manufacturing precision and stability of the mold must be considered to ensure the quality and performance of the plastic parts.
How does FirstMold manage color consistency for PBT parts across different production batches?
1. Material Quality Control: Ensure the quality and consistency of PBT materials to avoid product color instability due to material differences.
2. Mold Cleaning: Clean the mold before production to remove any impurities that may cause color changes.
3. Color Matching: Develop a reasonable color matching scheme based on client needs to ensure the uniformity of color across different batches.
4. Production Monitoring: Implement strict production monitoring to ensure that the parameters and processes during production meet the requirements, thereby ensuring the color stability of plastic parts.
What mechanical properties make PBT suitable for high-performance applications?
Specifically, the impact resistance and tensile strength of PBT are important factors for its wide use in high-performance applications.
The impact resistance of PBT is shown in its ability to absorb and disperse external impact energy, maintaining the integrity of the parts. The tensile strength is demonstrated in its ability to withstand large tensile loads, ensuring the stability and reliability of the parts.
Additionally, PBT also has good fatigue resistance and chemical corrosion resistance, further enhancing its performance for high-performance applications.
Can FirstMold integrate metal inserts into PBT molded parts?
Yes, FirstMold can manufacture PBT components with metal inserts. When making PBT molded parts, metal inserts can be used to enhance structural strength or add functionality. To ensure strong adhesion and structural integrity, the following process can be adopted:
First, the metal inserts need to be pre-treated to ensure their surfaces are smooth, free of impurities, and have the appropriate roughness to increase the bonding area. Next, before inserting the inserts into the PBT mold, they can be bonded to the mold surface using heat treatment or chemical adhesives. During the injection molding process, the PBT resin will fill the entire mold, including the metal inserts, forming a firm combination. Finally, during the cooling process, the inserts will be fixed in position, forming a complete molded part.
FirstMold has extensive experience and advanced technology to provide high-quality solutions for molded parts with complex structures. They offer a comprehensive production process and professional technical support to ensure the quality and performance of the molded parts.
How does FirstMold ensure dimensional stability of PBT parts during the production process?
1. Mold Design: Employ precise mold design, including appropriate gate locations, cooling systems, etc., to control the cooling time and stress distribution of plastic parts.
2. Material Control: Ensure the quality and consistency of PBT materials to avoid product dimensional instability due to material differences.
3. Temperature Control: Precisely control the temperature of the mold and plastic materials during the production process to reduce the risk of warping and shrinkage.
4. Post-processing: For plastic parts that require post-processing (such as electroplating, coating, etc.), ensure the stability and consistency of the processing process to avoid dimensional changes caused by the processing.
5. Production Monitoring: Implement strict production monitoring to ensure that the parameters and processes during production meet the requirements, thereby ensuring the dimensional stability of plastic parts.
Can FirstMold provide mold flow analysis for PBT projects?
Yes, FirstMold can provide mold flow analysis for PBT projects.
Mold flow analysis helps optimize mold design in the following ways:
1. Predicting Plastic Flow: By simulating the flow of plastic in the mold, it is possible to determine the optimal gate location, runner design, etc., to avoid defects such as weld lines, bubbles, and sink marks.
2. Cooling System Design: Mold flow analysis can predict the cooling speed and temperature distribution of plastic parts, thereby optimizing the design of the cooling system to ensure the stability of plastic parts during production.
3. Position and Shape of Inserts: Mold flow analysis can assess the impact of the position and shape of metal inserts on the flow of plastic, to ensure good adhesion between the inserts and plastic and to avoid defects around the inserts.
Through mold flow analysis, FirstMold can provide more precise mold design recommendations, improve production efficiency and product quality, and reduce production costs. This helps clients achieve better results in their PBT projects.