Optical Injection Molding (OIM) is a manufacturing technique that combines the precision of laser technology with injection molding efficiency. This excellent method creates parts with optical qualities and dimensional accuracy. The process involves heating and softening a polymer material with a laser beam before injecting it into a mold.
Glasses, Smartphones, and AR/VR headsets all have one thing in common: They depend on optical components. Precision polymer optics have great potential to replace conventional glass optics, but the latter cannot satisfy the need for smaller, lighter, and more affordable solutions.
Injection molding is an art in itself because numerous factors impact the quality of the molded part. The transparency of the materials is the primary issue in optical injection molding. A perfectly pure material guarantees the flawless optical function of the components.
This article addresses the complexities of optical injection molding (OIM), its advantages, uses, types of optical molding, and prospects. We’ll discuss how OIM has transformed manufacturing procedures and how it might spur further developments across various industries.
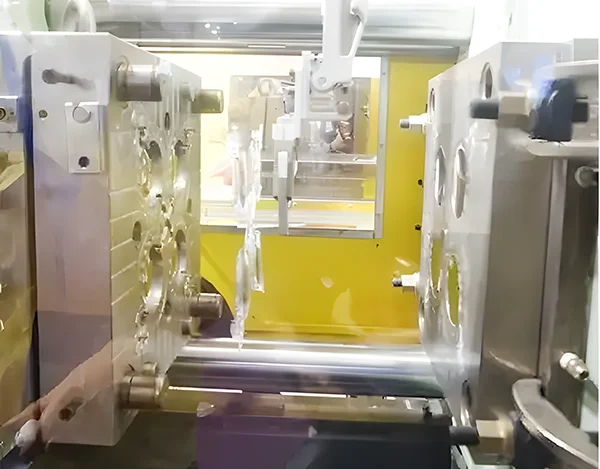
The Manufacturing Process
The production of polymer optics by injection molding relies on a complex interplay between material, man, machine, and mold. Experience and technology are necessary for a reliable injection molding procedure.
A significant benefit of employing polymer optics is the capacity to integrate optical and mechanical characteristics onto a single platform. The intricacy of the mold itself will increase based on the type of mechanical elements being taken into account. The mold is built to the negative of the final part. For example, the optical insert will be concave if the final optic has a convex surface.
Polymer optics can be coated using physical vapor deposition. Compared to coatings put on glass substrates, polymer substrates are applied at lower temperatures and have less endurance. Conductive, beam-splitting, antireflection, and reflective coatings can be specified for a broad range of polymer substrates. Antireflection coatings come in two varieties: single-layer MgF2 with an average surface reflectivity of roughly 1.5% from 450 to 650 nm or multilayer MgF2 with a surface reflectivity of less than 1% over a range of 450 to 650 nm.
Parts Produced Through Optical Injection Molding
Lenses
Lenses are critical components used in various industries. They come in different types.
- Aspherical lenses have a non-spherical surface profile, enabling them to reduce spherical aberrations. People use them in cameras, imaging systems, and VR/AR headsets.
- Plano-convex lenses have one convex surface and one flat surface. They are mostly used in headlights or magnifying glasses.
- Fresnel Lenses: flat lenses that use concentric rings to focus light, minimizing weight and thickness while maintaining optical performance. Ideal for solar concentrators and magnifiers
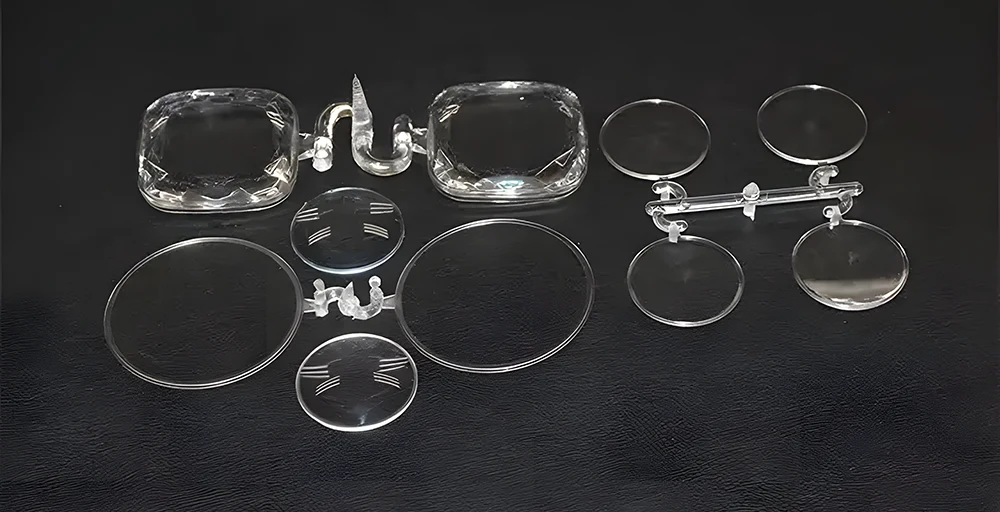
Light Guides
Light guides transport light efficiently while maintaining its quality and intensity. They use internal reflection to pass the
light until it reaches its target. Most of their design depends on the applications, with some having intricate shapes to alter the intensity and direction of light.
Applications in automotive dashboards, backlights for LCDs (TVs, Monitors, Laptops), communication devices like fiber-optic, etc.
Light Diffusers
Diffusers scatter light evenly across surfaces. This behavior creates a uniform light distribution minimizing glare. Diffusers use frosted, translucent, or textured materials to control the light along their path. Ideal for Displays (LCDs, OLEDs), Car headlights, and LED beams.

Reflectors
Reflectors redirect or focus light in specific directions. Most reflectors are designed to be flat, angled, or curved. Highly reflective materials like silver or aluminum are used to coat these lenses, ensuring minimal absorption. They are used in places that need light control and need to optimize efficiency. They are applied in car headlights, Mirrors in telescopes, microscopes, and lasers.
Display Panels and Windows
They are transparent covers allowing light and images to pass through for display. Besides,they also protect underlying components. They are coated to improve optical performance and made from materials like polycarbonate (PC), glass, or Polymethyl methacrylate (PMMA), and are useful in consumer electronics like smartphones, Medical equipment, Automotive Heads-Up Displays (HUDs), and windshields.
Optical Filters
They are intended to selectively regulate the light wavelengths that flow through them. Their functions are designed in different ways, such as bandpass filters (transmitting only a specific range of wavelengths), short pass filters (allowing shorter wavelengths to pass), or long pass filters (allowing longer wavelengths to pass). They can often be coated with thin films or made from plastics or glass.
They are applied in cameras, Spectrometers, scientific Instruments like; photometry, and colorimetry to filter out unwanted wavelengths and Laser systems.
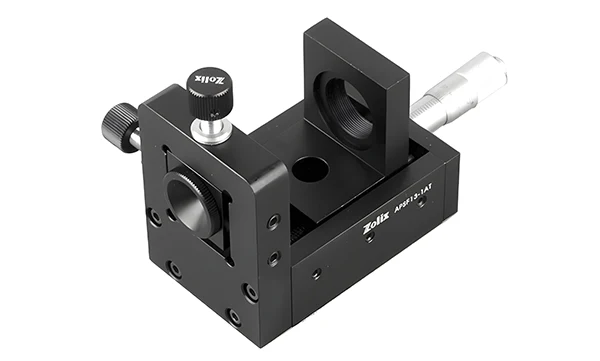
Optical Sensors and Detector Housings
They house and protect sensitive optical sensors used in detecting parameters. Besides, they protect them from external factors like moisture, dust, or mechanical damage that might alter the functionality of the sensors. They are made from materials that ensure accurate light transmission to the sensors without distortion.
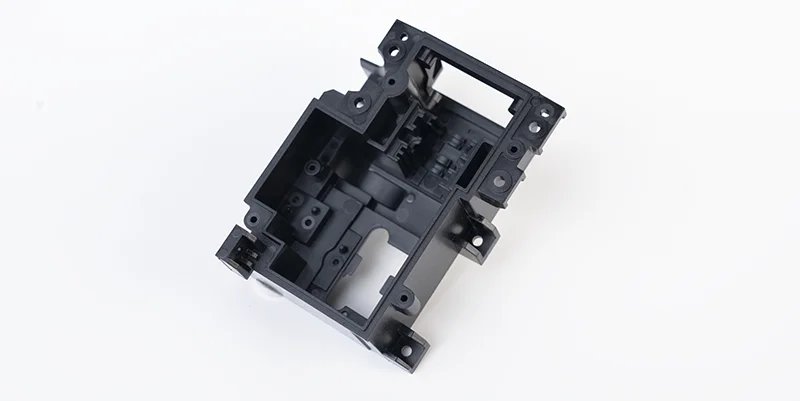
Ideal for:
Medical devices: Pulse oximeters, Blood glucose meters, Optical sensors.
Environmental Monitoring: Air quality meters and water quality sensors.
Industrial Automation Systems: Detecting position, presence, or distance of objects.
Essential Materials Used in Optical Injection Molding
Thermoplastic, polycarbonate, acrylic, and polystyrene are the primary materials used in Optical injection molding. Each of these materials is suitable for different optical applications because of the distinct properties that make them. Each thermoplastic has to undergo a specific evaluation before starting the design process.
Полистирол (PS)
Polystyrene is the most preferred material for precision molding due to its low shrinkage rate. This characteristic makes it a go-for-choice material for many designers because it can easily be crafted into intricate, detailed designs. Polystyrene features a refractive index of 1.59 and an 88.4% visible light transmission, similar to polycarbonate and acrylic.
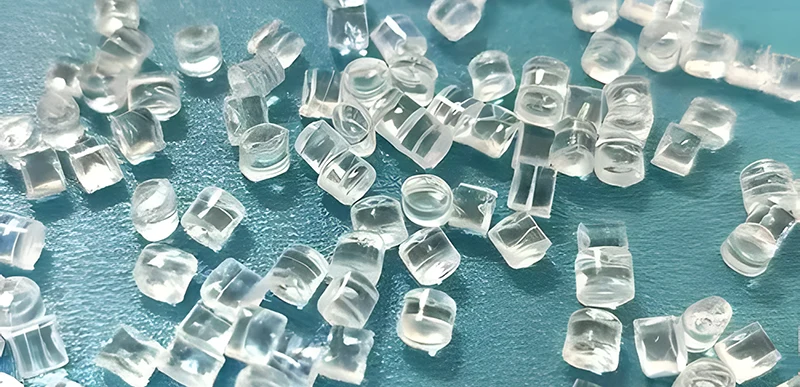
Поликарбонат (PC)
Polycarbonate (PC) is commonly used in precision injection molding processes. PC is advantageous in that it can easily be molded into complex geometry while maintaining its structural integrity. PC’s refractive index is estimated to be approximately 1.59, with an 84% visible light transmission and a 74.3% UV transmission rate. It has highly dependable optical properties like high impact resistance and outstanding optical clarity.
Polycarbonate is commonly used in several applications where durability and impact resistance are essential, such as vehicle headlamp lenses, LED illumination lenses, and safety eyewear.
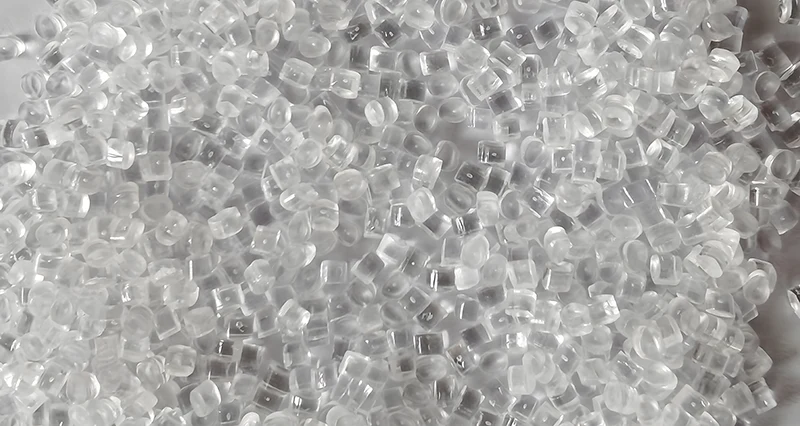
Acrylic (PMMA)
Acrylic is a material widely used in injection molding. Its excellent mechanical qualities are valuable for other production processes like CNC lathes and milling. Acrylic is known for exceptional scratch resistance and optical clarity. It boasts a refractive index of approximately 1.49 and a 92% visible light transmission rate. Compared to polycarbonate, acrylic can block almost all UV radiation with a UV transmission rate of just 4.82%. In optical applications where appearance is essential, it is mainly used as a lightweight substitute for glass. It suits consumer electronics and medical devices such as light guides, optical displays, and camera lenses.
Cyclic Olefin Copolymer (COC)
This new substance is renowned for its low moisture absorption and superior optical qualities. COC stands out among other materials like PS, PC, and PMMA because of its refractive index of 1.53 and 90% transmission in the visible spectrum. Many precision optical systems prefer COC because of its low dispersion and birefringence, which lead to less optical distortion.
Because of their excellent qualities, COCs can be used in many fields, including electronics, optics, and medicine. They are also used in high-demand goods, including optical films, lenses, and light guide panels.
Cyclic-olefin polymers (COPs)
COPs are closely related to cyclic olefin copolymers (COCs) but are often purer and offer a more refined property. They exhibit high transparency and optical clarity, usually comparable to glass. They have low optical distortion and a high degree of light transmission.
COPs are recognized for their exceptional optical qualities, with a refractive index of 1.53 and an astounding 91.6% visible light transmission. COPs are unique in transmitting visible light very well and have a low haze index of 1.78%, meaning that optical components lack haze.
Used in Medical Devices, such as endoscope components and diagnostic lenses; Precision Optics, including camera lenses, microscope optics, and optical sensors; and Lighting and Illumination, including light guides and LED lenses.
Comparison of Key Properties
Материал | Прозрачность | Долговечность | Optical Clarity | Общие приложения |
Поликарбонат (PC) | High (90%+) | Excellent (Impact-resistant) | Хорошо | Automotive lenses, LED lighting, safety eyewear |
Acrylic (PMMA) | Very high (92%+) | Good (Scratch-resistant) | Excellent (Low birefringence) | Consumer electronics, light guides, medical lenses |
Cyclic Olefin Copolymer (COC) | High (Comparable to glass) | Good (Chemical resistance) | Excellent (Low distortion) | Medical devices, camera lenses, optical data storage |
Полистирол (PS) | High (88-90%) | Moderate (Brittle, low-impact resistance) | Good (Clear but prone to distortion) | Optical packaging, light diffusers, disposables |
Cyclic Olefin Polymers (COPs) | Very high (Comparable to glass) | Excellent (Excellent chemical and moisture resistance) | Excellent (Very low birefringence) | Precision optics, medical devices, high-end electronics |
Types of Optical Molding
1. Precision Lens Molding
A special kind of injection molding is dedicated to producing precise lenses with tight tolerances. This process is crucial in places where flawless light refraction and transmission are essential, considering that even the slightest deviations can significantly affect output.
Found in cameras, microscopes, automotive headlights, and smartphone lenses

2. Micro-Optics Molding
Micro-optic molding is a highly specialized technique for producing miniature optical components with intricate features and small dimensions. Such techniques are necessary because the precision needed for these tiny optical parts is substantially higher than that of regular optics.
These components are crucial in the high-tech sectors of medical devices, fiber optic communication systems, and augmented and virtual reality (AR/VR) systems.
3. Light Guide Molding
It involves producing optical components specifically made to efficiently direct and distribute light in devices like LED lighting systems, automobile lighting, and display backlighting. Light guides guarantee uniform distribution throughout the component with minimal loss, glare, or distortion. The molding process produces perfect, clean surfaces to improve light transmission and attain precise control over light paths. Any imperfections can stop the light from flowing correctly and result in unpleasant glare, reflections, or light loss.
They are primarily used in headlamps, interior car lights, smart devices, etc.
4. Diffuser Molding
A specialized optical injection molding technique makes light-scattering parts that minimize glare or offer uniform lighting. These parts disperse light evenly over a surface, preventing hot spots and harsh reflections. Diffusers often have micro-textured surfaces or uniquely designed geometries that assist in scattering light uniformly. During molding, surfaces are created to control the diffusing angle and light spread to balance light transmission and diffusion.
Diffusers provide uniform light distribution in lighting and display technologies, essential for performance and visual comfort. They are widely used in LED panels, monitors, TVs, and automotive interior lights.
5. Birefringence-Controlled Molding
A highly specialized optical injection molding technique is employed when it’s necessary to reduce the double refraction of light or birefringence. The term “birefringence” refers to a material’s capacity to refract light in several ways depending on the polarization direction. Birefringence can occur due to stress or strain during the molding process. Low-birefringence materials are most preferred to manage molding conditions effectively. This is because it can affect the precision of the optical components due to the optical aberrations.
Special polymers used in this case are cyclic olefin copolymers (COCs) and cyclic olefin polymers (COPs), which have a low tendency to cause birefringence under stress.
Used in parts such as endoscopes, MRI scanners, Lidar sensors, smartphone lenses, etc.
6. Multishot (Two-Shot) Molding
It is also called two-shot or multi-component molding, which involves injecting two different materials into a single mold to improve optical components’ structural and functional features. Multiple materials, which may be a combination of optical and non-optical materials, are molded together with durable housing. For example, optical lenses, cameras, and sensors are molded together.
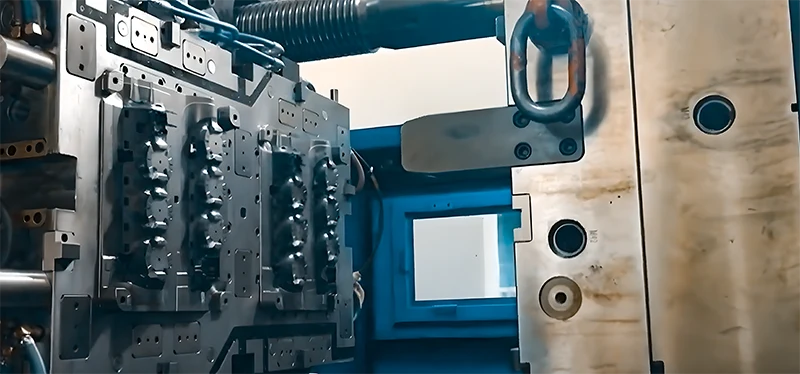
Advantages of Optical Injection Molding.
1. Permits the cost-effective manufacture of vast volumes of optical components, significantly lowering costs per unit, particularly when automation is used.
2. Eliminates the need for laborious post-processing by supporting complicated designs, such as micro-optics, freeform geometries, and aspherical lenses, all in a single molding phase.
3. Lightweight plastics like polycarbonate (PC) and cyclic olefin copolymers (COCs) can reduce weight without sacrificing strength or optical clarity.
4. It permits multishot molding, fusing optical clarity with other materials to produce products with multiple uses, such as lenses with integrated housings or optical coatings.
5. Provides a large selection of materials with specific qualities (such as UV protection and scratch resistance) designed for various uses in consumer electronics, automotive, and medical fields.
Future Trends of Optical Injection Molding
1. Advanced Materials for Enhanced Optical Performance
Developing new polymer materials with enhanced optical characteristics will continue to drive innovation. Future materials, such as improved Refractive Index Control and Eco-Friendly Materials, may perform better under extreme conditions.
2. Micro-Optics and Nanophotonics Molding
Advancements in micro-injection molding will make it possible to produce micro-optics with extraordinarily tight tolerances.
The demand for tiny optical components keeps rising, especially in the consumer electronics, AR/VR, and medical device industries.
3. Integration with Industry 4.0
Industry 4.0 technologies, such as IoT, AI, and machine learning, are integrated to optimize production processes. OIM processes can be highly automated, with robots handling tasks and reducing human error. Data on several facets of the OIM process can be gathered and analyzed using sensors and data analytics tools. Digital twins of OIM equipment and procedures can be created to facilitate virtual testing and simulations, enabling optimization before actual implementation.
4. Growth in Medical and Biophotonics Applications
Biophotonics and medical devices are expected to require more optical components in the future. High-precision and dependable optical components will be needed for non-invasive imaging, laser treatments, and wearable health monitoring systems.
Заключение
Optical injection molding has brought tremendous change to the manufacture of optical components. Many industries are adopting this technique because it can produce optical components at a fraction of the cost and time. With innovative trends like smart manufacturing and advanced materials on the horizon, the possibilities are unlimited. Whether it’s creating sophisticated optics for medical equipment or lightweight lenses for smartphones, OIM is making it all happen.